This is Google Earth photo of the lot that Amanda and I purchased in Ruidoso Downs, New Mexico. We're in the house with the dark roof in the middle of the picture. The Rio Ruidoso runs along the south edge of our lot (look for the dense trees) and the road is along the north edge.

I actually started the shop project back in July. Originally I thought I would make all the buildings out of load bearing straw bale. New Mexico is a little fussy about load bearing straw bale, though, and I would be importing the straw from Texas or Colorado. Enter compressed earth block (CEB).
CEB is essentially adobe construction, but the blocks are pressed into shape using a manual or hydraulic press. The earth mix has minimal moisture going into the press, so the block need not dry in the sun like traditional adobes.
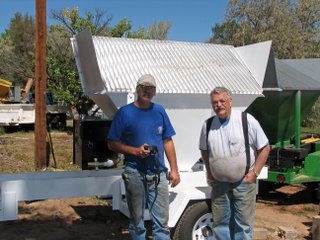
After much research, I decided to buy a machine from Powell and Sons in San Ysidro, New Mexico (
http://www.adobemachine.com/). William Powell and his sons (see photo of Powell and one son with my machine) agreed to build me a machine with no engine and no hydraulic pump, instead setting the hydraulics up to run off of my compact tractor. The money saved on engine and pump allowed me to upgrade to an automatic machine that presses 2 blocks per minute for as long as the hopper contains dirt. I'm sure we'll see a lot more of the press in the months to come.
After settling on a general building technology, I designed the shop and sketched out a house and guest house using Sketchup (
sketchup.google.com). This is a free and very helpful 3d drafting program. It does pretty much everything, including modeling the shadows at a given time of year and at a given latitude, longitude, and elevation. Below is a picture of the basic sketch.

Obviously, it needs some work. But the sketch allowed me to do three things:
1. Orient the three buildings for optimum solar gain (the house will be passive solar and the shop and guest house will gain some heat from the sun)
2. Obtain the best possible view from the house, keeping with maximum solar gain.
3. Fit everything in on the lot while still allowing us to live in the current (and hopefully short-lived) house and shop.
All of the existing buildings will either be razed or removed when all is said and done.
At this point in the design process, I took a hiatus to address two issues that impacted the eventual building projects. The first of these involved moving an access easement on the property which was in the way of the shop footprint. Easements are tedious, so the only other thing I am going to say on the subject is that our neighbor, who happens to be a surveyor, was infinitely helpful with moving the easement. Thanks, Paul!
The second issue is more interesting. Our building project is not going to be certified green built, but I did want to minimize the impact on the planet while building (hence building the walls out of earth). To this end, I built a biodiesel reactor to supply the compact tractor (and hence the block press) and my pickup with biodiesel. For those of you who know nothing about biodiesel, see: www.journeytoforever.org/biodiesel_make.html. As you can see from the pictures, the reactor would make Rube Goldberg proud. It does work, however, and, with a little help from the grease traps of Denny's and the Log Cabin Restaurant, I am now running both tractor and truck on my own biodiesel.Back to the shop.
After the biodiesel hiatus, I submitted my plans to the State of New Mexico for contemplation and blessing. They hemmed and hawed (not being used to building methods that do not involve traditional framing) and finally approved the shop plans. Which brings me to today, October 4, 2006, when my official building permit arrived in the mail. So tomorrow I am off to start earth work to prepare for the foundation, to prepare for the walls, to prepare for the roof... This last picture shows the area where the shop will be located and the funny red building that will be torn down as soon as, and not one day later, the shop is finish. (Okay, I may have actually started the earth work before I received my building permit in the mail.)

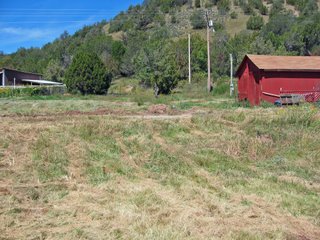
More will follow.